
Last Updated on: 10th November 2024, 02:29 am
There may be one kind of emulsion, but not another. How does this happen? The reality is that all that is emulsified by quality producers is working but sometimes shops use the wrong product in a certain printing form.
For instance, if you print with water-based ink and do not use an emulsion specifically formulated for this purpose, you can have problems. This is a simple fix: swap the product simply for a more acceptable emulsion.
More frequently, however, it is a process failure that causes errors and prevents a stencil from working properly. Sometimes, activities are small or ignored and can make all the difference when fixed or tweaked.
1. Drying Screens Properly:
The emulsion consists mainly of liquid; a 40% solid emulsion consists of 60% water, and before exposure, the humidity needs to evaporate from the stencil.
Want to Boost Your Print Shop Revenue?
Schedule a free consultation
The excess water can prevent the stencil from curing when the coated screen is not fully drained, causing many problems, such as loss of durabilities, premature press breakdown, poor quality, inadequate water or solvent and grips.
In addition, this excess water blocks the cross-linking of the stencil during the process of exposition. In diazoic and dual-cure products, this is especially true. Even photopolymer emulsions can be completely healed after growth. You have to monitor the atmosphere by keeping the drying area as dry as possible to ensure best practice in screen drying.
2. Check the Humidity Level:
A 32% moisture level is best. That is to say, the more the drier, the more better. The first measurement takes place by means of the humidity test in the drying area using an affordable hygrometer, which costs between $10 and $35 online or in a home improvement shop.
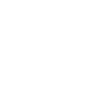
Do you have printers? Are those printers sitting idle?
Become a Print-on-Demand dropshipping app like Printful or Printify. Dropship your merchants' orders.
Unlimited Merchant stores. Dropship and Fulfil Merchants' orders. Manage merchant invoice, sales commission, etc. Merchants sell the designed products in shopify, etsy stores, etc.
Know moreThis instrument tests the temperature of the air. The relative moisture (RH) is a significant number if all screens are simultaneously coated and in the desiccation space.
When you have 50 screens that are coated with 40 percent solid emulsion, that is 60 percent of the water in each glass. You know how big or how many dehumidifiers are required to keep the room dry.
If you have low moisture and use a small heater to keep the temperature steady of 70°F -75°F degrees, screens will dry quickly and completely.
Ensure your dehumidifiers can drain into a floor drain or empty on a regular basis. Otherwise, the water they capture out of the air will evaporate back into the air and stencil.
3. Without stencil you lose detail:
Detail and resolution are the roles of the stencil. Based on the volume and thickness of the wire, you can determine the amount of ink required.
The quantity of stencil material on the panel is known as mesh emulsion (EOM), which is measured as an emulsion degree over the mesh thickness. Optimum EOM is measured at 10% to -18%.
The difference between poor EOM at 1% and a strong EOM of 15% is easy to see and feel and it is not difficult to figure out with better resolution what will be written more in-depth.


Boston based custom slide sandal maker has become $10 Million company using an online designer and unique growth marketing.
Read moreTo achieve the right EOM, you require proper methods of coating. Second, maintain a smooth round edge of your manual coater.
Emulsion of scrapes with a smooth surface. The round edge covers the mesh, fills the mesh openings, and produces an EOM. Proper methods of coating will proceed to the end of the coating cycle on the squeegee side.
Where do you require EOM? Where is it appropriate? A thickness gauge is the simplest way to calculate EOM. Most shops have too thin stencils that cause poor printing, resolution, and even longevity with a decreased print run.
Not all shops can or should invest in a gauge of thickness. However, you can feel the lip of the stencil and the mesh by simply running the finger on the substratum of a formed panel. The EOM is probably too thin if you can’t feel this.
4. Improper Curing Leads to Loss:
Most shops concentrate on a short presentation period as their key attribute when looking at the overall care of stencil.
An underheated plug may be the beginning of a variety of issues such as a press failure, damaged reliability, loss of the boundary concept, and problem recovery that can contribute to time and benefit losses.
Too many shops use a test-and-error method to identify and create screens. To assess the duration of exposure before the time set near enough without real determination.
5. Best Practice to Cure Stencil:
Using an exposure meter or a 21-step scale on-screen to follow best practices for the assessment of a complete stencil remedy. If you build the screen, the rinse the scale with an inkjet film to a solid phase 7.
Weh you use a direct to screen device, a solid 6 is best. If a higher or a lower number emerges, the time may then change accordingly and shows over or underexposure.
There is no guessing with this process; just complete stencil cure. For each shop, a 21-step scale is a resource.
We often blame the emulsion for such issues as inadequate detail and resolution, when it may simply be the unit of the exposure unit.
The artwork has one job: to create an illuminated shadow. You want a single column of light, like a spotlight on a stage, to get a narrow shadow. You get a blur shadow if several lamps come from different angles.
6. How does Image Exposure work?
The light must be single or in a column to create this crisp shadow. Collimate light is a form of light found in single-point lights such as a metal halide or LED point.
In comparison to a multi-faceted light, this collimated light permits the desired resolution like fluorescent pipes.
Conclusion:
The right emulsion is the secret to a successful and efficient printing process for your shop. By defining and verifying do not make searching more difficult.
Using the right software to make sure the screen operation is running smoothly.
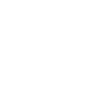